1. 行业痛点催生变革动力
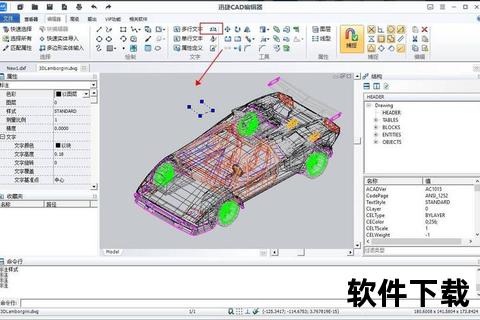
在智能制造与数字化转型浪潮中,通用型CAD软件逐渐显露出适配性瓶颈。某船舶设计院的案例具有典型性:其工程师在使用通用软件进行舱室布局时,需要重复绘制80%的标准化组件,导致设计周期延长40%。这种效率损耗在医疗设备、航空航天等高度专业化领域更为明显,根据Gartner 2023年行业报告显示,垂直领域企业因软件适配问题造成的年均效率损失高达120万美元。
定制化CAD的突破性在于将行业know-how转化为数字资产。以建筑信息模型(BIM)领域为例,上海某设计院开发的装配式建筑专用CAD系统,通过预制构件库和智能拼装算法,使标准户型设计时间从72小时缩短至8小时。该系统深度整合了GB/T 51269-2017建筑信息模型分类标准,实现设计规范自动校验,错误率降低90%以上。
2. 技术架构实现精准适配
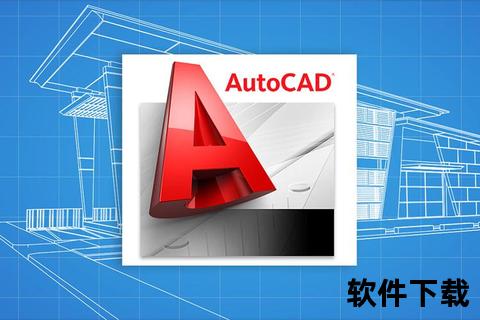
参数化设计引擎的突破为定制化提供了技术基础。达索系统开发的CATIA定制平台采用模块化架构,允许汽车制造商植入空气动力学仿真模块。某新能源汽车企业通过该平台将风洞实验次数从300次降至50次,每款车型研发周期缩短6个月。这种深度定制能力源于对NURBS曲面算法的改进,使复杂曲面的计算效率提升400%。
云原生技术重构了CAD软件的交付模式。Autodesk Forge平台为石油装备行业打造的定制方案,通过微服务架构将钻井平台设计拆分为127个独立功能模块。工程师可根据具体井深、地质条件组合功能包,设计迭代速度提升5倍。该平台对接AWS IoT Core的实时数据接口,使设计方案能动态响应钻井现场的传感器数据流。
3. 领域知识驱动价值跃升
在医疗器械领域,定制化CAD系统正突破传统设计边界。强生医疗开发的骨科植入物设计平台,集成了20万例临床手术数据构建的形态数据库。通过机器学习算法匹配患者CT影像,系统可自动生成适配度达98%的假体模型,将传统手工建模所需的3周时间压缩至48小时。这种深度定制使翻修手术率从12%降至3%以下。
汽车轻量化设计凸显定制软件的计算优势。宝马与ANSYS合作开发的复合材料专用CAD系统,采用多尺度建模技术精确模拟碳纤维铺层效果。系统内嵌的材料数据库包含2,300种复合材料的力学特性,结合拓扑优化算法,使某车型B柱减重35%的同时保持碰撞安全性。这种领域专精设计使整车研发成本降低18%。
4. 生态协同构建竞争壁垒
工业软件巨头正在构建定制化开发生态。西门子NX Open API开放了2,800多个接口,支持第三方开发者接入专业算法。某航空发动机制造商基于此开发了叶片冷却通道自动生成插件,将原本需要2个月的设计验证周期缩短至72小时。生态化发展模式使软件复用率达到70%,显著降低定制开发成本。
开源社区催生新型协作模式。Blender基金会发起的CAD Sketcher项目,聚集了来自32个国家的开发者共建参数化设计模块。其建筑版块整合了IFC 4.3标准,支持从概念设计到工程量清单的全流程贯通。这种众包开发模式使专业版块的迭代速度提升3倍,维护成本降低60%。
数字化浪潮正重塑制造业竞争格局,定制化CAD软件已成为垂直领域的技术支点。从参数化引擎的技术突破到领域知识的数字化封装,从云原生架构的灵活部署到开发生态的协同创新,每个技术维度都在创造独特的价值空间。未来,随着数字孪生技术的深化应用,定制化CAD将向实时仿真、自主优化方向演进,为行业用户构建更具韧性的创新基础设施。这要求软件开发商持续深耕垂直场景,将物理世界的行业规律转化为数字世界的算法优势,最终实现设计效率与创新质量的协同跃升。